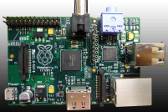
Raspberry Pi
Richard Wilson travelled to Wales and discovered an electronics sector with world-class companies, cutting-edge university research and with aspirations to grow
I travelled to Wales to do some mountain-walking and discovered a two-week festival which was bidding to raise the profile of Wales as a centre for electronics technology.
Technologies were on show at 40 events, with companies across the region ranged from world-class semiconductor process technology and robotic systems, to MEMS sensors and systems for defence and aerospace.
Companies taking part included Sony, General Dynamics and semiconductor wafer producer IQE, as well as nano-health researchers from Swansea University.
Facility visits, seminars and exhibitions were open to student and the general public to raise the profile of the Welsh electronics sector.
There were also networking events to connect global companies operating in Wales with the local supply chain.
“Wales can already claim credit for an amazing array of enabling technologies, although that’s not always widely recognised,” said Ian Menzies, chair of ESTnet, the electronics and software technologies network for Wales. He is also senior director in Wales of General Dynamics.
Menzies pointed to a recent UK innovation survey which showed that just over 40% of Welsh firms with over 10 employees are ‘innovation active’ which means they regularly introduce new or significantly improved products and processes or engage in innovation projects.
“If we can build energetically upon the work to date and nurture a new culture of innovation this could earn the Welsh economy billions of pounds extra and create thousands of new high-quality jobs,” he said.
Most recent figures from the survey show that 22.5% of Welsh company turnover was generated from new or significantly improved products and services, with 5.8% of total turnover coming from products that were totally new to the market.
Among the home-grown Welsh companies showcasing their work was Cardiff-based IQE, a manufacturer of specialist compound semiconductor wafers which are supplied to chip makers world-wide.
IQE supplies over 50% of the world’s RF epitaxial wafers, which are used to fabricate radio front-end ICs for mobile phones. IQE possesses the largest independent manufacturing capacity of compound semiconductor epi worldwide, and as a result, is able to achieve enhanced economies of scale, helping to build wafer capacity and cost structure needed to grow the GaN market.
“We are beginning to see very significant traction for GaN occurring in the compound semiconductor industry, across a wide range of applications” said Drew Nelson, president and CEO, IQE, who won the lifetime achievement award at the Elektra Awards 2013.
The company is now creating in its Welsh facility a production capability for gallium nitride (GaN) on silicon wafers which is expected to be an important technology for volume markets such as smartphone power amplifiers.
IQE has recently signed a licence agreement for gallium nitride (GaN) on silicon wafer with M/A-COM Technology. The agreement gives the Wales-based wafer producer access to RF and microwave IP for gallium nitride (GaN) on silicon technology.
M/A-COM has also signed an epitaxial (epi) wafer supply agreement with IQE allowing the compound semiconductor wafer producer to manufacture GaN-on-silicon epi at 4, 6 and 8-inch diameters in high volume for RF applications.
According to IQE, this agreement will deliver GaN RF products with “breakthrough bandwidth and efficiency at mainstream 8-inch silicon cost structures.”
The deal means that Wales will be a source for large diameter wafer manufacturing capabilities to support mainstream, commercial adoption of GaN technology.
“We are nearing a watershed moment for the RF and microwave industry, promising breakthrough performance for compound semiconductors and leveraging large-scale silicon production facilities that operate at orders of magnitude greater economies of scale,” said John Croteau, president and CEO, M/A-COM.
According to IQE’s Nelson, the agreement will bring “decades of high volume production experience to create the necessary supply chain needed to accelerate GaN adoption.”
As part of the innovation festival IQE was one of a number of companies taking part in an event at St Asaph, North Wales designed to establish technology partnerships with other Wales-based electronics firms.
Also at the event in St Asaph, Microvisk invited visitors to hear about its pioneering micro-viscometer, based on novel, patented MEMS (micro electromechanical system) technology used in medical sensors.
General Dynamics’ EDGE innovation centre at Oakdale, Gwent is organising facility visits, while the electronics and software technologies network for Wales (ESTnet) holds its software exhibition at Cardiff City Stadium.
Research in Wales has also contributed to the sophisticated sensor technology used in the Bloodhound high speed car, bidding to break the land-speed record.
The University of Swansea is one of a group of UK universities taking part in a £2m research project to develop safer, cheaper and more sustainable new materials for solar cells.
The “PVTeam” project aims to develop new active materials for photovoltaic solar cells based on abundant and low cost elements, says the university.
Specifically, the research objective is to replace key elements such as gallium, indium, cadmium and tellurium with abundant non-toxic alternatives, “while developing and implementing processes compatible with large-scale manufacturing in the UK”.
Another event took place at the Sony UK Technology Centre at Pencoed, Bridgend.
Sony’s UK Technology Centre was in the headlines last year when it manufactured more than a million Raspberry Pi educational computers.
The computer boards have been sold by distributor element14, which partnered with Sony UK TEC.
“The strategic decision to bring the Raspberry Pi back to the UK and partner with the electronics giant Sony UK TEC has a number of benefits from bringing the manufacturing centre closer to the head office, reducing transport costs and supporting UK mass scale manufacturing,” said element14.
“In a little under a year we have created one million units at our site in Pencoed, Wales which has resulted in us generating 40 local jobs,” said Steve Dalton OBE, managing director of Sony UK Technology Centre.
“The work done by all parties has acted as a significant milestone in the UK manufacturing industry, which ultimately helps to support and grow the UK economy.”
According to Edwina Hart, Minister for economy, science and transport in the Welsh Government: “We have first class academia for research and development, cutting-edge technologies and pioneering people and businesses leading the way. Promoting further innovation is a top priority for the Welsh Government and we have key programmes in place to achieve that.”