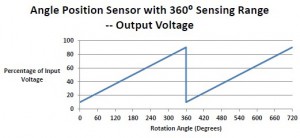
Figure 1
Angle position sensing is the measuring of the degree of rotation of an object about a central axis.
As with any sensor type, the aim is to represent a physical or mechanical characteristic in a format, usually electrical, that can be understood, interpreted and which can be used as an input to a microcontroller circuit.
In some cases, a physical characteristic is mechanically converted to a second physical characteristic and then measured.
For example, a rack and pinion scheme could be utilised as a means of measuring linear travel with an angular position sensor, by first converting the linear motion into a rotational movement.
Angle position sensors are available in many forms and utilise various technologies but generally speaking these sensors are highly versatile and can designed into many industrial and high reliability applications.
We are seeing a large growth in angle position sensor usage in automotive, off-road vehicles, agricultural and commercial equipment, and industrial automation.
Typically these are applications which require a product that is suited for operation in harsh environments where dust, dirt, extreme temperatures and moisture are factors.
In addition to an International Protection (IP) rating, angle position sensor products typically are offered in contact, or non-contact configurations.
For applications that exist in harsher, rugged conditions non-contact sensors are extremely applicable due to vibration and abrupt movement not affecting performance. There is also the added benefit of a very long lifespan of non-contact sensors.
These benefits make angle position sensors an increasingly important design option for several industrial applications requiring longevity and of course durability. Of course, these types of sensors can serve as a great alternative to potentiometers.
Other similar devices, such as rotary encoders essentially do the same thing.
Hall effect-based rotary encoders and Hall effect angle position sensors essentially perform the same function using a magnetic field, as defined by the Hall effect. Traditional absolute rotary encoders however, differ from Hall effect angle position sensors. Yes, they detect rotation, position and angle, but they do so by using an LED transmitter, slotted disc and a photo sensor.
The encoder is able to convert rotational motion into electrical signals by shining light through each column of slots on the disc; the photo sensor then reads the level of light or dark areas and then translates this into an electrical data stream which can be input to the microcontroller system for analysis and storage.
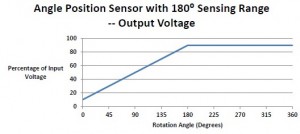
Figure 2
Essentially, the main difference being the sensing circuit makes use of magnetic readings instead of measurement levels of light and darkness. It is important to note that traditional encoder accuracy is largely dependent on resolution, which is determined by the number of columns and rows of slots. The higher the resolution, the more precise the detection of movement is.
General Application Examples:
- Forklift Position Sensing: Measures the angle of the forks on a forklift truck.
- Trailer Hitch Position Sensing: used in both commercial and agricultural equipment. The tilt or angle of a trailer hitch is detected to help hook up to trailers and various attachments.
The Occupational Safety and Health Administration (OSHA) in the US has reported that the three primary causes for tip-over accidents on forklifts are excessive speed when the machine is turning, raised unbalanced load and collision with an overloaded object.
With such a large group of forklift manufacturers having a need to account for these issues several sensor components have been utilised to help manage these risks. Gear tooth sensors have been integrated to count the rotation on a gear or wheel to limit and monitor speed.
Magnetic proximity sensors have also been designed into forklifts to sense whether a seat belt is fastened or a door is shut, ensuring a driver is properly secured while operating. Hall or reed proximity sensors can also detect hydraulic fluid levels.
Angle position sensors have also found their way into forklift applications, detecting the angle and position of the forks.
This particular application can prevent unbalanced loads, or limit operation of the machine when a load is improperly balanced or positioned.
The same technology is also utilised in the wheels controlled by the steering function. Having an accurate position reading on the steering wheels can prevent the machine from being accelerated while wheels are turned too far to the right or left, causing unexpected manoeuvers and unsafe operating conditions.
Like all components, sensors continue to evolve and become more advanced in terms of capabilities, performance, form factor and overall integration into several applications. We expect to see their usage and popularity with application designers to increase and angle positions sensors are just one example of the trend.
When you consider the level of performance, along with excellent tolerance for harsh conditions and extremely long lifespan, it is no surprise that these products are gaining attention, particularly with compact designs that make them easier and less restricting to design into products. Look for angle position sensing to expand even further in the near future.
Ryan Eder is marketing manager at Cherry Industrial Solutions
Richard Wilson