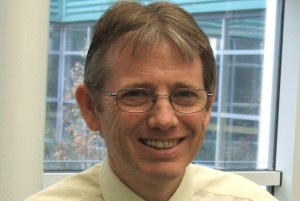
Pete Dorey
The European EMC defence standard 59-411 can help with achieving electromagnetic compatibility for COTS military systems, writes Pete Dorey.
The electromagnetic compatibility (EMC) risk assessment process described in Defence Standard 59-411 contains four key steps to assess whether any protection, such as shielding racks and filters, is needed to reduce equipment susceptibility to harsh defence electromagnetic environments and to enhance compatibility with sensitive systems such as military radio.
Define the electromagnetic environment
Once this environment definition is known, the adequacy of the military off-the-shelf/commercial off-the-shelf (MOTS/COTS) EMC performance can be evaluated.
The target electromagnetic environment is usually specified in a User Requirement Document (URD) or System Requirement Document (SRD), and is likely to be one of the default electromagnetic environments described in Def Stan 59-411, such as a ship below-decks environment.
However, it may also be specified for a unique purpose, to ensure compatibility with specified systems, or tailored to a specific environment.
Evaluation of EMC compliance
All non-exempt MOTS/COTS equipment must carry the CE mark of European directives, but its presence alone is not enough to identify levels of EMC performance to which the equipment must comply. This must be identified from the manufacturer’s EU Declaration of Conformity, test report, certificate or specifications.
It is best practice that a copy of the EMC test report or certificate is obtained to confirm the limits applied during testing, in order to ensure the equipment’s suitability for military use. However, obtaining the evidence of EMC compliance is often a major challenge.
Using the guidance in Def Stan 59‑411, a ‘gap analysis’ process can be used to determine whether the MOTS/COTS EMC compliance evidence is more or less stringent than the Def Stan 59-411 test limit. Any shortfalls identified also help to specify the degree of additional protection that is required, such as shielding or filter attenuation.
During this process, it is imperative to identify the test methods and account for them as part of the comparison. This can be a time consuming, costly and complex exercise, so the use of specifically designed gap analysis tools is recommended.
Functional criticality
The risks identified during the gap analysis process must now be compared to the criticality of the equipment and platform environment impact in which the COTS/MOTS equipment will be used.
If any unacceptable risks are identified, they must be mitigated. For example, if the equipment has a critical function itself, adequate immunity is required. If the equipment is co-located with other sensitive critical equipment, adequate emission control is required.
Once the functional criticality process has determined the unacceptable risks, they must then be mitigated.
Mitigation of unacceptable risk
There are two options for risk mitigation, either:
• Retest the MOTS/COTS equipment to determine compliance with Def Stan 59-411. This is technically a good approach, as any additional protection can be properly specified and over‑protection will be avoided. However, the disadvantage is the cost of the additional required testing.
• Remedial re-design can be achieved by adding the appropriate protection ‘barriers’ to reduce the coupled RF fields or currents that the equipment could be exposed to, or could emit, to below the levels it was originally required to meet.
Many manufacturers now offer suitable RF shielded racks and enclosures for this purpose, which allow the MOTS/COTS equipment to be housed without modification therefore preserving the validity of its CE marking. Additional filters and transient protection can also be accommodated within the enclosure. If the equipment itself is modified to achieve EMC, it is considered to have become ‘modified off the shelf’ equipment and needs to meet the EMC Directive with CE marking as a ‘new apparatus’ in its own right.
Something that could be overlooked is that the current UK EMC regulations (SI 2006 No.3418) implementing the EMC Directive 2004/108/EC do not have a specific exemption for defence equipment, whereas the previous regulations did, under Article 346 of the Treaty of the European Community.
This has led to some confusion among designers and manufacturers, with some presuming that a ‘blanket’ exemption applies to military equipment.
However, the applicability of CE marking to military equipment was clarified by the European Commission in April 2012 with the statement: “Equipment which falls within the scope of the Radio & Telecommunications Terminal Equipment Directive, EMC Directive or Low Voltage Directive, shall be compliant with the applicable Directive(s) and bear CE marking.”
Defence contractors must therefore ensure that any manufacturers or suppliers they use understand and comply with these rules.
Member states can exclude defence equipment from the scope of European Union procurement regulations and Directives pursuant to Article 346 (ex.296) of the Treaty on the Functioning of the European Union on the basis of the protection of national security interests.
This is not a decision for the manufacturer. Further guidance on the compliance of military equipment with the EMC Directive was published by CENELEC in report TR50538 in 2010.
In April 2016, a new EMC Directive 2014/30/EU and EMC Regulations will come into force, but do not affect the requirement for military equipment. Applying the EMC Directive to defence equipment requires careful management to avoid unnecessary duplication of compliance-testing – once for Def Stan 59-411 and once for CE marking, which will incur additional costs.
However, testing can be minimised by using the gap analysis process to establish in the technical documentation the equivalence between Def Stan 59-411 and the MOTS/COTS standards. This in itself can be a time consuming and costly exercise and often takes users away from their core expertise or comfort zone.
Due to the complexity of performing gap analysis, such a partner could offer a low risk, and ultimately low cost solution to deal with defence EMC requirements. It will ensure that the resulting products are legally placed on the market and acceptable for delivery, particularly for high-value projects.
Writer is Pete Dorey, a principal EMC consultant at product testing and certification organisation, TÜV SÜD Product Service
Richard Wilson