The aluminium capacitor is a common feature of power supplies, since it is the most suitable for functions such as energy storage and low- or high-frequency filtering. Unfortunately, aluminium capacitors are also often the components most prone to failure: the operating lifetime of an aluminium capacitor will tend to determine the operating lifetime of the entire power supply, writes Marcin Chelminski of Future Electronics.
This means that designers have to take great care when calculating the parameters of aluminium capacitors to choose the most appropriate part for their device.
The choice of capacitor also has to balance cost against performance: after magnetic components, aluminium capacitors are often the most expensive passive components in a power supply.
The reliability of an aluminium electrolytic capacitor is generally measured by its expected life in use.
Minor factors that affect their life include humidity, vibration and heat transmitted through the printed circuit board patterns.
But three other factors have a greater effect on useful life, these are: ambient temperature, ripple current and applied voltage.
The basic application guidelines for aluminium capacitors say that operating temperature, applied ripple current and applied voltage should always stay below the specified maximum allowable values.
But these guidelines do not provide enough information to enable power‑supply designers to optimise for long operating life.
For this, they need to estimate the effect on lifetime of variations in operating conditions within the maximum allowable limits.
By accurately estimating the effect of changes in operating conditions, designers can extend the lifetime of aluminium capacitors in any given application.
The latest generation of dedicated power-supply capacitors, which benefit from the most recent advances in design and materials, can offer long lifetimes of up to 15 years in a surprisingly wide range of operating conditions without incurring the cost ultra high reliability capacitors.
Aluminium capacitor failure modes
Aluminium capacitors implement a variety of functions, depending on their position in the circuit.
As an input buffer in an AC-DC converter, an aluminium capacitor provides energy when the mains input voltage is too low, or stores energy when it is too high.
As an output buffer, an aluminium capacitor performs filtering and acts as a current sink for an inductor.
In operation, these capacitors can fail in a number of ways:
- catastrophic failure occurs when the capacitor completely breaks down, due to a short or open circuit.
- degradation occurs when the capacitor continues to function, but its performance has deteriorated to some extent.
In the case of degradation, for instance, the device’s capacitance might fall over time. Whether the change in value is acceptable or not depends on the requirements of the application. If it is unacceptable, the device has effectively failed.
A short circuit between the electrodes can be caused mechanically, by shock, vibration or stress on the leads.
It can also be caused electrically, by the application of a pulse current or voltage which exceeds the rated maximum value.
There can be various causes of an open circuit. For instance, if the capacitor is subjected to too high a force at the time of mounting, the connection between the lead wire and the tab could be twisted or distorted.
High temperature is also dangerous, either by operating at a temperature above the rated maximum, or through exposure to excessive heat transmitted through the circuit board’s tracks, which vaporises the capacitor’s electrolyte.
Similarly, exposing the capacitor to excessive ripple current causes its internal temperature to rise, drying the electrolyte.
A fall in capacitance and increased power losses due to high equivalent series resistance (ESR) occur when:
• a reverse voltage is continuously applied
• the capacitor is subjected to a very high number of charge/discharge cycles
• applied current exceeds the maximum rated ripple current.
Optimise for conditions
Standard load life test limits applied to aluminium capacitors (at their rated voltage and maximum rated temperature) typically measure the elapsed time until the capacitor suffers a 20% or 30% decrease in capacitance from its initial value, a 200% or 300% increase in loss tangent (a measure of the power losses attributable to the dielectric), or a 200% increase in leakage current – whichever occurs first.
These standard limits provide a quick but rough means of comparing the performance of competing devices. But they do not necessarily reflect the requirements of any given application.
So to optimise the lifetime/cost trade-off and find the best possible capacitor for a specific power supply, the designer must calculate the expected life of capacitors under evaluation in the expected operating conditions of the application.
Before doing so, it is worthwhile considering how the operating conditions of the power supply might be modified so as to minimise the hazard to any aluminium capacitors on the board.
The electrical characteristics of aluminium electrolytic capacitors are more sensitive to temperature than those of other types of capacitors, because the properties of the liquid electrolyte in aluminium capacitors, (such as conductivity and viscosity) are strongly affected by temperature.
To reduce the device’s exposure to high temperatures, the designer needs to understand the flow of thermal energy through it (Figure 1).
Inside the dotted line, all the materials are at the device’s junction temperature (Tj); outside the dotted line is the ambient temperature (Ta).
The heat generated inside the dotted line is carried outside it by convection, radiation and conduction.
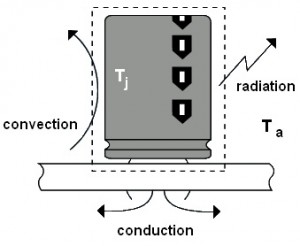
Figure 1: the three ways in which heat escapes from a power supply’s capacitor
If the designer can implement a means to improve the heat flow out of the capacitor, its expected operating lifetime will be extended.
Indeed, according to the Arrhenius theory, the life of an aluminium capacitor doubles with every 10°C fall in ambient temperature.
Such a fall has a direct effect on the designer’s lifetime calculation when the heat generated by resistive losses (for instance, in timing circuits) is negligible.
The basic method of cooling a capacitor is to mount it in free space. The natural circulation of air around the device will provide sufficient cooling for most applications.
If this is not enough, a heat sink will increase the flow of heat from the device. The most common type of heat sink is an aluminium extrusion attached to the closed end of the capacitor. An alternative is a semi-circular extrusion designed to clamp to the case of the capacitor.
Whichever capacitor is used in a power supply, the designer can ensure that the device survives for its average rated lifetime by regulating the temperature, ripple current and applied voltage to within the manufacturer’s specified limits.
Marcin Chelminski, central applications engineer, Future Electronics (Poland)
Richard Wilson